U.S. Navy Cuts Aircraft Carrier Building Costs by $2 Billion
Over four years, HKPO CEO Jennifer Ralston oversaw this effort to comply with Congress’ mandate to trim money from a massive budget on an end product to protect the freedom of the United States. Working at the Navy Yard in Washington, DC, as program manager, Mrs. Ralston directed training and coaching exercises designed to help the Navy identify opportunities for process improvement.
In the end, Ralston’s leadership helped the Navy comply with the congressional mandate to find $2 billion savings on the building process. The process improvement standards are now being applied to other areas of the military including NAVAIR and Maritime.
The National Defense Authorization Act of October 2006 requires the United States Navy to have a force of not less than 11 operational aircraft carriers. In 2013, the Navy was tasked with building a new carrier CVN-79 (later named the John F. Kennedy), yet cut $2 billion dollars from the construction budget. No small task for a project with a $13 billion-dollar budget. Congress realized if did not find a savings now then the amount they would need to trim would continue to inflate.
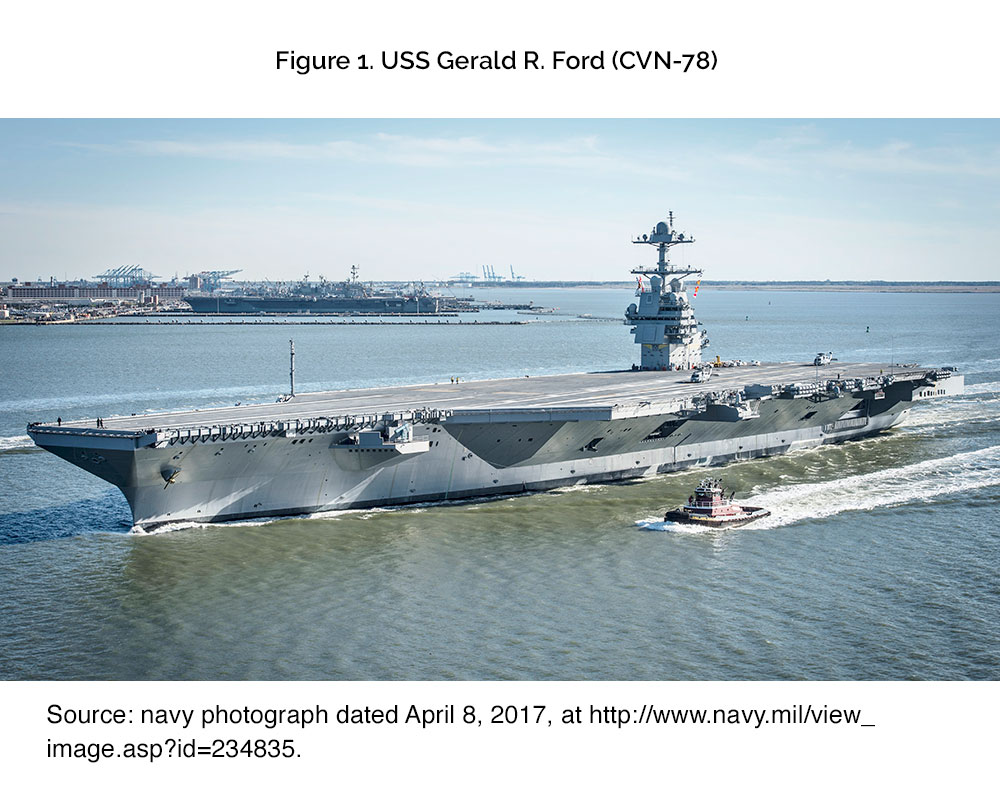
Having just built CVN-78 (the Gerald R. Ford), the Navy assembled a team to take a critical look at the construction of that ship. Over four years, HKPO CEO Jennifer Ralston oversaw this effort to comply with Congress’ mandate to trim money from a massive budget on an end product to protect the freedom of the United States. Working at the Navy Yard in Washington, DC, as program manager, Mrs. Ralston directed training and coaching exercises designed to help the Navy identify opportunities for process improvement. She ran multiple Process Improvement projects to look at how each part of CVN-78 could be built more efficiently. “When you approach construction of an aircraft carrier that is massive in size and budget, the only way to determine where and if you can streamline the process is to look at the component parts before you access the whole.”, said Mrs. Ralston. “We are very grateful for this amazing opportunity with the Navy and working with prime contractors like Genedge and Computer Science Corporation.”
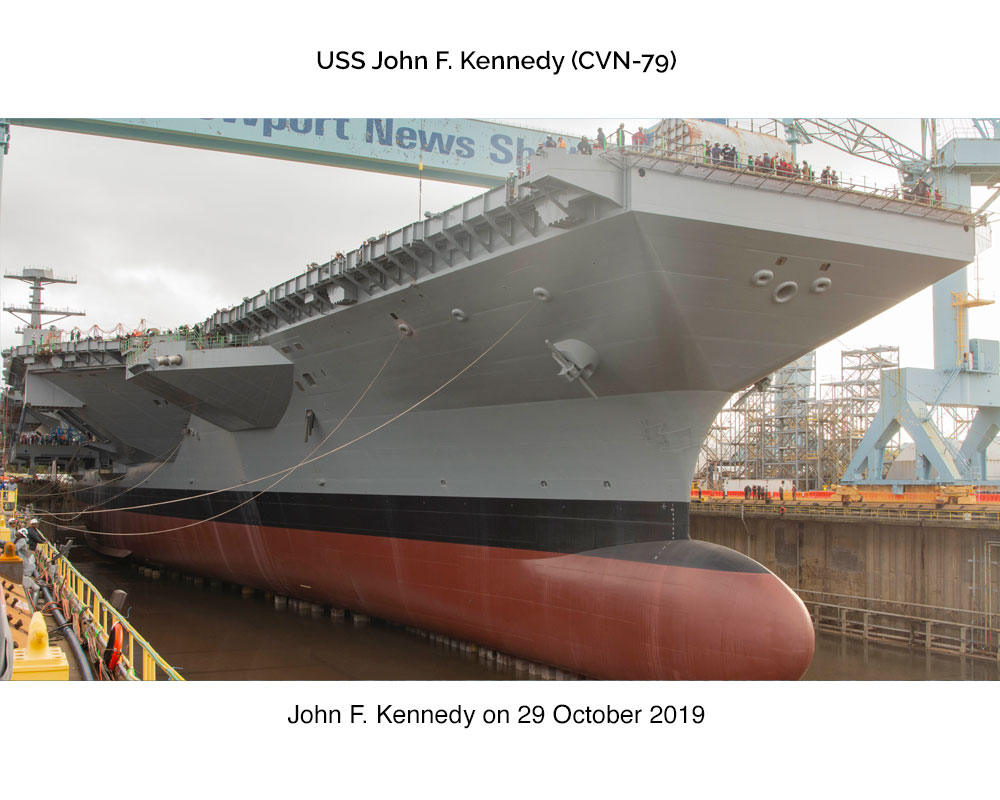
One of the main challenges when building a ship of this size and complexity is that it takes years to complete. During that time technology advances, thereby rendering systems obsolete. Mrs. Ralston and her team discovered that systems were being tested too early that by the time the ship was assembled, those systems had to be replaced. In addition, testing these systems was slow and redundant when the system was tested again once the ship was assembled.
“We had to have some real discussions with the Navy about how they approached testing during construction,” she said. “Why not wait and test the systems closer to when the ship is ready so that you are only testing once?”
In addition to overhauling the testing process, improvements had to be made to the actual way the ship was constructed. Again, breaking down the ship down to its component parts was key. From the Congressional Research Service (CRS) Report Navy Ford (CVN-78) Class Aircraft Carrier Program: Background and Issues for Congress,
“The ship is being built with an improved shipyard fabrication and assembly process that incorporates lessons learned from the construction of CVN-78.”
This was achieved by outfitting ship modules before they were stacked together to form the ship. If problems were found once the ship was already assembled, it would need to be taken apart before it could be fixed and then reassembled. Digital ship renderings allowed for a greater understanding of the inner workings of the ship before piecing it together.
Shifting work earlier in the build process allowed for any changes to be made early on.
“Front-loading the work ensured that once it came time to assemble the ship, all that remained was getting it in the water,” said Mrs. Ralston. They also found ways to order materials and parts quickly and economically saving both time and money. Citing the CRS Report again, “…the Navy and shipbuilder have made fundamental changes in the manner in which the CVN 79 will be built to incorporate lessons learned from CVN 78 and eliminate the key contributors to cost performance challenges realized in the construction of CVN 78.”
In the end, Jennifer Ralston’s leadership helped the Navy comply with the congressional mandate to find $2 billion savings on the building of CVN-79 and eventually CVN-80 (the Enterprise). The ship cost $11.341 billion rather than $13.341 billion. What is more, the process improvement standards are now being applied to other areas of the military including NAVAIR and Maritime. Mrs. Ralston and a team of Lean Six Sigma Experts are uniquely positioned to take experiences like this one and apply the learnings to today’s unique process improvement needs. Now more than ever it is important to not overlook the small, incremental changes that can make a big impact. HKPO Lean Six Sigma Experts bring over 50 years of combined experience and industry resources to a variety of complex environments and with that comes time-earned excellence in every aspect of their work.