American Red Cross Saves $60 million on Blood Donation Operations
Using the Lean Six Sigma approach to process improvement, HKPO CEO Jennifer Ralston developed operational changes designed to reduce the number of donor reactions after giving blood, therefore ensuring a donor’s positive experience. These changes comprised of standard work guidance for staffing, materials and equipment, and work sequence.
By focusing on the donor, understanding how the set-up happens and then implementing steps for making processes flow smoothly, she and her team saw a 50 percent decrease in the rate of presyncopal reactions in donors.
Creating a positive experience for someone who is donating blood may seem like an impossible task for an activity that requires a needle. However, when processes are in place to make people feel comfortable before, during, and after they donate blood, the experience can be over quickly and somewhat painlessly. Toward that end, in 2008 the American Red Cross examined how a blood drive is set-up impacted the donor experience. They studied high school blood drives in the Pacific Northwest, Mid-Atlantic, New England and Midwest of the United States.
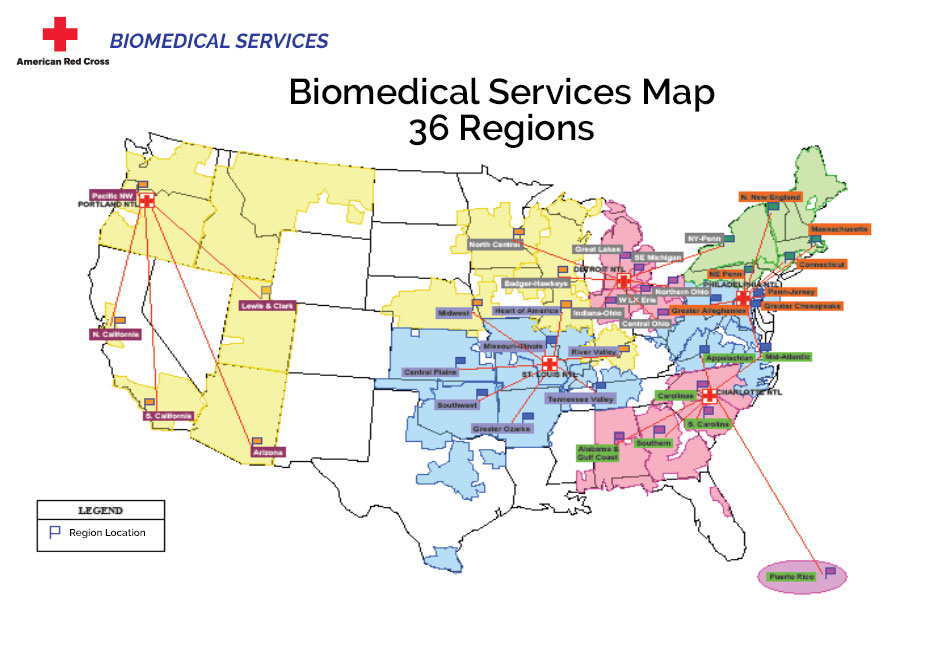
During this time, HPKO Lean Six Sigma Experts CEO Jennifer Ralston was the Director of Process Improvement for the American Red Cross. In this capacity, she observed many blood drives to determine efficiency. One thing she often saw was that if a person developed presyncopal symptoms after giving blood (dizziness, lightheadedness) and subsequently lost consciousness, in full view of other donors, it created a domino effect. In short, if one donor passed out, then others would follow. When this happened, time and attention was taken away from incoming donors who needed to be prepped for giving blood, thereby slowing the entire process down and creating a less than optimal donor experience.
Using the Lean Six Sigma approach to process improvement, Mrs. Ralston developed operational changes designed to reduce the number of donor reactions after giving blood, therefore ensuring a donor’s positive experience. These changes comprised of standard work guidance for staffing, materials and equipment, and work sequence. They addressed having enough beds and interview areas for the expected number of donors and outlined layouts for optimal drive set-up. One key change removed the waiting area from in front of the venipuncture (puncturing of the vein) area, while another defined a standard collection process flow from arrival to recovery. By focusing on the donor, understanding how the set-up happens and then implementing steps for making processes flow smoothly, she and her team saw a 50 percent decrease in the rate of presyncopal reactions in donors.
“The changes were small and incremental,” said Ralston. “Just flipping the beds around so they were end-to-end rather than side-by-side gave the donors a more private experience and greatly diminished the domino effect.”
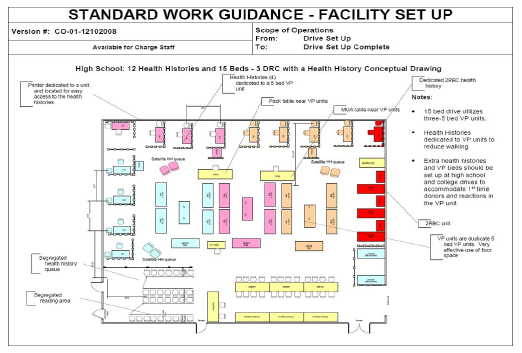
In order to understand if these guidelines would affect any change, the Red Cross studied donation-related reactions experienced by 16-and-17-year-olds during a 7-month period (Sept. 2007 – March 2008; Period 1) and then again from (Sept 2008 to March 2009; Period 2) after the operational changes had been implemented. They then compared the results of the two periods.
Over the course of a year, the American Red Cross tracked $60 million dollars in savings under Mrs. Ralston’s leadership. Since leaving the American Red Cross to start her own company, Jennifer Ralston together with Chief Operating Officer Nekol Tseklenis and a team of Lean Six Sigma Experts are uniquely positioned to take experiences like this one and apply the learnings to today’s unique process improvement needs. Now more than ever it is important to not overlook the small, incremental changes that can make a big impact. HKPO Lean Six Sigma Experts bring over 50 years of combined experience and industry resources to a variety of complex environments and with that comes time-earned excellence in every aspect of their work.
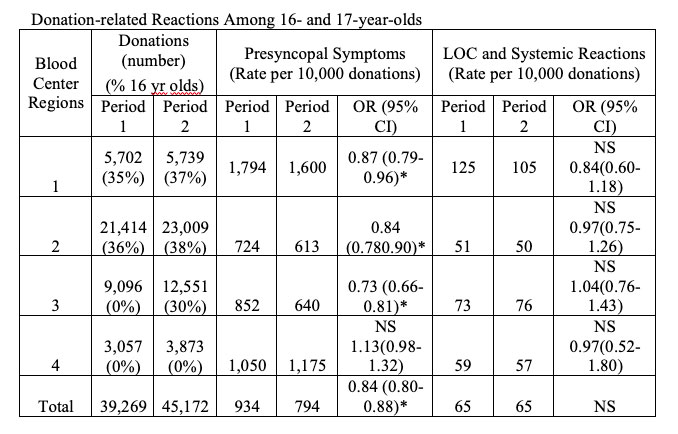
Overall, the standardized drive work process accounted for a significant decrease in reactions among 16-and-17-year-old donors in Period 2 compared to Period 1. The improvement was seen in three of the four regions and was entirely accounted for by a significant decrease in the rate of presyncopal reactions (the aforementioned dizziness and lightheadedness). It is worth noting that even though the number of donors increased in Period 2, the rate of loss of consciousness and major system reactions (eg. Injury, prolonged recovery) still decreased by over 50 percent once the work process was implemented.